Weaving a viable future for our local fabrics
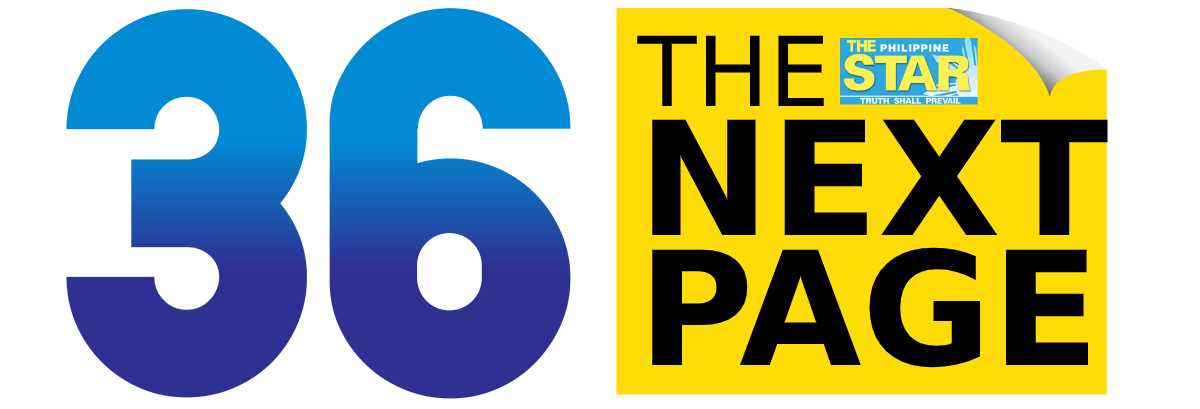
Face masks emerged as an indispensable article of clothing during the pandemic, becoming the first line of protective wear for everyone. But at a time when we needed protection desperately, we did not have sufficient supply of face masks let alone the local capability to replenish them in grocery shelves. That problem unmasked our inability to fully secure the basic needs of Filipinos during a crisis.
To address this urgent need, there was a push to develop cloth masks for community use; the necessity demonstrated how society needed to accelerate research, development, and innovation in the area of textiles. Weaving communities undertook heroic efforts to pivot and use their woven products as face masks. However, not all such masks measured up to official standards for community use cloth masks, particularly in terms of their water repellent function.
A noteworthy exception was the handwoven face masks created by Likhang Maragondon which were compliant with the interim government guidelines. The Department of Science and Technology’s Science for Change Program also funded a project that developed the formulation and the machine used to make cloth masks in rural settings. Communities in Abra and Mindoro produced exquisite handloom woven fabrics that were converted into face masks. The handloom woven textiles were treated to render them water repellent while also keeping them breathable, raising the quality of the fabric and consequently highlighting the value of science and technology to textile innovation.

At the height of the lockdowns, we also did not have the capacity to test, let alone do research and development (R&D), on face masks and protective wear. However, in 2020 the government funded the Medical Textile Testing Lab, which is now partially operational.
Contrary to popular impression, R&D and innovation in Philippine textiles hinged on creativity, inclusivity, and sustainability have been around even before the inception of the Philippine Textile Research Institute (PTRI) in 1967. They were pushed by the industry at the onset and supported by the government later on, but things have not been any better in recent years, until now.
The work on sustainability builds on the efforts from the 1970s that started looking at local materials like abaca, pineapple leaf, banana, ramie, among others, as viable fabrics. The Philippines has 66,000 hectares and 449,000 hectares planted to pineapple and banana, respectively, and the PTRI blends these fibers in a bid to create sustainable production. Natural dyes have also been developed from 100 plant sources; some of these dyes are converted into powder through natural dye hubs like the one in Bauan, Batangas. Standards are now being developed to safeguard this burgeoning industry.

The DOST-PTRI has forayed into producing natural textile fibers for technical applications through the Nonwoven I Innovation program, where natural textile fibers are used for footwear and wearables, filtration purposes, and even for automotive applications. The nonwoven pineapple leaf insoles of the Lakat shoe line by Creative Definitions are an example. Local textiles have also been used as anti-ballistic protection and as a substitute for the imported gear used in the battle dress uniforms of our armed forces.
Creativity in Philippine textiles does not just relate to design, color and form, but also strikes a balance between these elements and practical function.
In all these, we do a careful review of the life cycle of our products to help create a circular textile economy, a more eco-friendly system of textile development and to ensure the upcycling of post-industrial waste.
Inclusivity measures are meant to make sure that no one is left behind. The Seda Pilipinas program, for instance, was a bid to reestablish the local silk capability of the Philippines to fill the unserved 90%, or around 9,000 kg, of local silk requirements. The program sought to prevent the unregulated entry and trade of silk to protect our own Barong and pina textiles in Aklan. This year, the Philippine Silk Road, the very first silk reeling facility in Claveria, Misamis Oriental, was inaugurated, and is now producing silk yarns from 31 cocoon producers in eight cocoon production hubs in Northern Mindanao. This completed the chain of production, beginning from the commercial silkworm hybrids developed by the largest silkworm germplasm in the Philippines that were then put to the test and to actual commercial use.

Genomic studies at the Philippine Genome Center and UP Diliman also paved the way for the marker-assisted breeding of Philippine silk. The program helped revitalize silk cocoon production in the Cordilleras and this year established a silk reeling facility in Kalinga. In 2020, the revived silk cocoon production helped 17 cocoon producers in Kapangan, Benguet. These efforts are complemented by the silk throwing facility in Bago City, Negros Occidental, that develop plied and thicker yarns for other silk products, apart from the sheer fabrics that silk is known for. At full capacity, these facilities can reduce the country’s silk requirement gap from 90% to around 50%. A Philippine Silk Summit is set to happen November this year, where the Bayo X Seda Pilipinas collection will be launched, making local silk products more accessible to consumers via the retail clothing company Bayo’s physical stores.
Government funding for Philippine textile R&D has never been in a better state than today, and with the resurgence of national pride in our own textiles, materials and crafts, there is much hope indeed for the industry.
Creativity in Philippine textiles does not just relate to design, color and form, but also strikes a balance between these elements and practical function. The fusion of science and the production of our handloom woven textiles has allowed for the rollout of developed yarns and natural dyes and their eco-treatment, helping rebrand handloom woven textiles while remaining conscious of their cultural significance. The participation of weaving communities was purely voluntary, and interventions were carefully introduced not to replace or undermine traditional techniques or designs, but to provide innovative options. This program has given rise to jazzed-up binakol patterns and the weaving of silk and natural-dyed cotton yarns for the inabel of Paoay, Ilocos Norte; the use of natural dyes like Philippine indigo, talisay, achuete, yellow ginger and coffee pulp in the weaving of silk and pina fibers in Aklan; the use of other natural dyes for the black and red ikat-dyed abaca of the t’nalak of Lake Sebu, South Cotabato; and the playful and masterful rendition of the hinabol of the Higaonons in Impasug-ong, Bukidnon. The communities were challenged to weave wider widths (more than the usual 24-30 inches of fabric), use colors other than their traditional palettes, and employ more eco-friendly treatment technologies in preparing yarns and fiber.
In 2018, the first Regional Yarn Production and Innovation Center (RYPIC) was inaugurated in Miag-ao, Iloilo; a second center will open by the end of 2022, and a third one, in Mindanao, in 2024. These yarn production centers are designed to provide yarns for our weaving communities, and, per Republic Act 9242, to make available Philippine tropical fabrics as materials for the uniforms of government officials and employees. With one RYPIC at a time, we will soon be able to fulfill this volume requirement.
Two new programs of the DOST-PTRI — the Digitalization of the Handloom Weaving Industry and SAFATOS (Shoes and Footwear, Accessories Research and Development Towards Omnibus Textile Solutions) — will eventually provide a registry of weavers, looms, and weave designs that will help the government profile the industry and direct needed interventions. It will also provide a means to authenticate designs and a framework for the authentication and protection of such work.
The strides that have been achieved by our own textile researchers, our engineers and their processes and machines, our partner textile fiber producers on the ground, our handloom weavers, textile and garment manufacturers, and fashion designers in the creative sector are all linked toward creating a textile manufacturing industry with an inclusive, sustainable and creative future. While science, technology, and innovation are the drivers of the local textile industry and crafts for them to advance in both the domestic and international fronts, we can only go so far as scientists and researchers. In the end, public support remains paramount. Government funding for Philippine textile R&D has never been in a better state than today, and with the resurgence of national pride in our own textiles, materials, and crafts, there is much hope indeed for the industry. The evolution of our local artisan fabrics is not only a testament of our capability to produce our own, but, more importantly, an assurance that by working together, we can always do better.